【获奖论文回顾】第21届银奖论文:复杂钛合金阀体的铸造工艺研究
《复杂钛合金阀体的铸造工艺研究》发表在2018年第12期《铸造》杂志上,并获得第二十一届(2018年度)“福士科杯”论文银奖。
该篇论文对船舶复杂钛合金阀体的铸造工艺进行了深入的研究,通过分析船用复杂结构钛合金阀体铸件的结构、技术要求和铸造难点,制定了一套完整的铸造工艺方案,并结合ProCAST有限元分析软件进行了工艺优化,设计了更加合理的浇注系统,完善了铸造缺陷控制的方法,解决了铸件的成形问题,为复杂钛合金阀体铸造提供了更优的解决方案。
复杂钛合金阀体的铸造工艺研究
随着船舶工业的快速发展和国家对造船行业的高度重视,钛合金在海洋环境中具有良好的耐腐蚀和抗冲蚀性能,是海洋运输及其有关应用的理想结构材料。越来越多船用管路系统零部件采用钛合金材料。除此之外,与不锈钢相比,钛合金具有密度较低、比强度高、膨胀系数小、塑韧性好和抗裂纹扩展速率低等优点。
本文针对某造船厂阀体的结构特点及使用要求,进行了铸造工艺设计和工艺优化,生产出质量合格、尺寸精度满足要求的复杂结构钛合金阀体铸件。
1.1 产品的结构特点
该阀体铸件采用牌号为ZTC4材质的铸造钛合金,图1为该复杂结构阀体的平面图。其结构是由四个单阀体组成的联合体,每个阀体由中空的圆管连接,左侧的单阀体横向带有法兰,右侧的单阀体横向封闭,结构较为复杂,在日常的工程应用中较为少见。该阀体铸件整体尺寸为910 mm×255 mm×255 mm,阀体的壁厚为6 mm,十处法兰的厚度为24 mm,四个单阀体的中心距分别为215 mm、230 mm和215mm,铸件重量为43.0kg。
1.2 铸造难点
阀体铸件尺寸公差等级为CT6级,而四个单阀体的中心距尺寸决定着整个部件的装配精度,且四个单体的内腔后期不进行机械加工,完全由铸造工艺来保证四个单阀体的中心距尺寸,查表知三个尺寸的允许公差为±0.5 mm,难度较大。
阀体外围结构为法兰,尺寸较厚大,而四个单阀体及连接管处于中间的位置,尺寸较小,厚度尺寸仅为法兰厚度的1/4,铸件的薄厚不均且分布情况也不利于铸造成形及质量控制,法兰部位容易出现气孔、缩松等缺陷。
1.3 铸造工艺方案的选择依据钛合金的化学特性及铸造特性,以及本阀体铸件的选材和结构,采用数控加工石墨型+真空自耗电极熔炼+离心铸造的工艺方案。
2.1 铸件的布局与缩尺的设置
根据铸件的结构特点,铸件的对角线长度约为873.5 mm,熔炼设备选用ZNL200型真空自耗凝壳炉,其熔化量为200 kg,离心盘直径为1400 mm,确定一炉浇注两件,浇注工艺设计见图2。据文献记载,综合考虑铸型的阻碍以及合金成分等因素,同时结合铸件实际的结构和尺寸,拟定该铸件各个方向的缩尺均为1%。
2.2 铸件的浇铸系统设计
考虑到单阀体的壁厚6 mm和法兰的厚度24 mm,确定内浇道从四个圆形法兰处引入, 内浇道截面积为432.5 cm2,横浇道截面积为174.4 cm2,S横∶S内=1∶2.5,符合钛合金石墨型工艺设计的要求,即采用开放式的浇注系统。浇注系统布置如图3所示。
2.3 分型面的确定与型、芯的划分
图4所示为阀体铸件的工艺装配平面图及立体示意图。外皮2#、3#芯和5#芯子均采用数控机床进行加工。
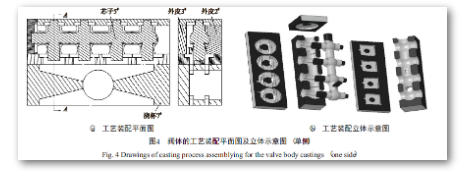
2.4 数值模拟
基于上述的工艺模型,还有浇杯、坩埚和炉壳内壁等三维模型,对本铸造工艺方案进行ProCAST有限元分析数值模拟。其中缩松、缩孔等铸造缺陷的模拟结果和铸件收缩引起尺寸变化的曲线,如图5所示。
从模拟结果的图片可以看出,①厚大的法兰存在较多的缩松缺陷;②按左图分别取特征点1和特征点2,特征点1曲线从工艺偏移量1.8 mm逐渐收缩,终凝固后与理论值还差1.0 mm,特征点2曲线同特征点1曲线;特征点1、2的正负并没有实际意义,只是参照不同而已。可见铸件各部位的收缩变形并不一致,而且关键尺寸与图纸尺寸偏离较大。
2.4.1 原因分析
①远离中心的法兰较厚大,由薄壁向厚大的法兰进行充填和补缩不畅通。
②石墨抗压强度大于铸件凝固时产生的应力,使铸件收缩受到阻碍,造成理论尺寸预期存在偏差。
2.4.2 工艺改进措施
①在四处方形法兰和其余两处圆形法兰连接若干条直通浇道,且浇道的等效截面直径大于两倍小壁厚。
②各处法兰的背面都增加0.5 mm至1.0 mm的工艺补贴量。
工艺方案修改后再次进行ProCAST有限元分析,模拟结果未发现上述铸造缺陷,且收缩变形造成的尺寸问题也得到了较好的解决。综上所述,该铸件在实际凝固过程中,各个方向的收缩量并不一致,应该对拟定的缩尺进行必要的修正,即长度方向上的缩尺减小至0.7%,其余两个方向可以保持原缩尺不变。
2.5 石墨型的数控加工
采用数控机床加工石墨型实现了石墨型加工的一次质的飞跃,彻底地解决了普通机床加工质量不受控、一致性较差,组装复杂石墨型、芯干涉面较多和修复困难等问题。本例对较为复杂的外皮2#、3#芯和5#芯子采用数控机床进行加工,这些芯子的具体位置可参考图4。下面列举了外皮2#芯和5#芯子的三维图形,如图6和图7所示。组型过程见图8。
2.6 石墨型的真空除气
石墨多孔,且孔隙发达,吸附能力较强,即使在空气中也会吸收大量的水分和其他气体,因此必须对石墨型进行除气处理[5]。除此之外,真空高温焙烧还能够降低松散的灰分颗粒的含量,从工艺角度切断造成气孔和夹杂的来源。石墨型的真空除气处理工艺曲线如下图9所示。
2.7 真空熔炼和离心浇注
熔炼和离心浇注是在ZNL200型真空自耗凝壳炉内进行的,熔炼前,关闭炉门,拧紧放气阀,通高压电、抽真空,待真空度低于6 Pa时,起弧熔炼,熔炼结束前1 min,启动离心装置,熔炼结束后,坩埚自动翻转进行浇注,离心转动保持5~10min,随炉冷却至300℃,停止抽真空,打开放气阀,浇注过程结束。熔炼工艺曲线和离心铸造工艺曲线分别见图10和图11,两个工艺曲线皆取熔炼起弧时为参考零点。
浇注结束后,对铸件进行打磨、探伤、喷砂等处理,处理后的铸件如图12所示。该铸件表面完整、光滑,无裂纹、缩松等缺陷。因此,采取上述工艺方案浇注后,终获得了成形完整的钛合金阀体铸件。经过现场检测,阀体的关键尺寸(215±0.5)mm、(230±0.5)mm和(215±0.5)mm 分别为215.37 mm、230.41 mm 和215.24 mm,其误差均在规定数值范围之内,其余尺寸也符合铸件的精度要求。检验其他各项技术指标同样均满足相关技术协议的规定。
(1)采用数控加工石墨型+真空自耗电极熔炼+离心铸造的工艺方案可以生产出高质量的复杂结构钛合金阀体铸件,为今后铸造此类铸件提供了指导和借鉴。
(2) 中小型钛合金铸件的缩尺一般取值1%,由于本阀体铸件横向串联分布有四个单个阀体,此方向的缩尺建议修改为0.7%。
(3) 厚大的法兰背面有较大的收缩变形,需增加工艺补贴,工艺补贴量取0.5~1.0 mm。
摘自2018年度论文,全文请见《铸造》2018年12期
联系我们
中国机械工程学会铸造分会
联系人:王云霞(论文评选)
电话:024-25855720
手机:13940361719
邮箱:wangyunxia@foundrynations.com
联系人:王 鑫(征文)
电话:024-25855793
手机:18842811962
邮箱:wangxin@foundrynations.com